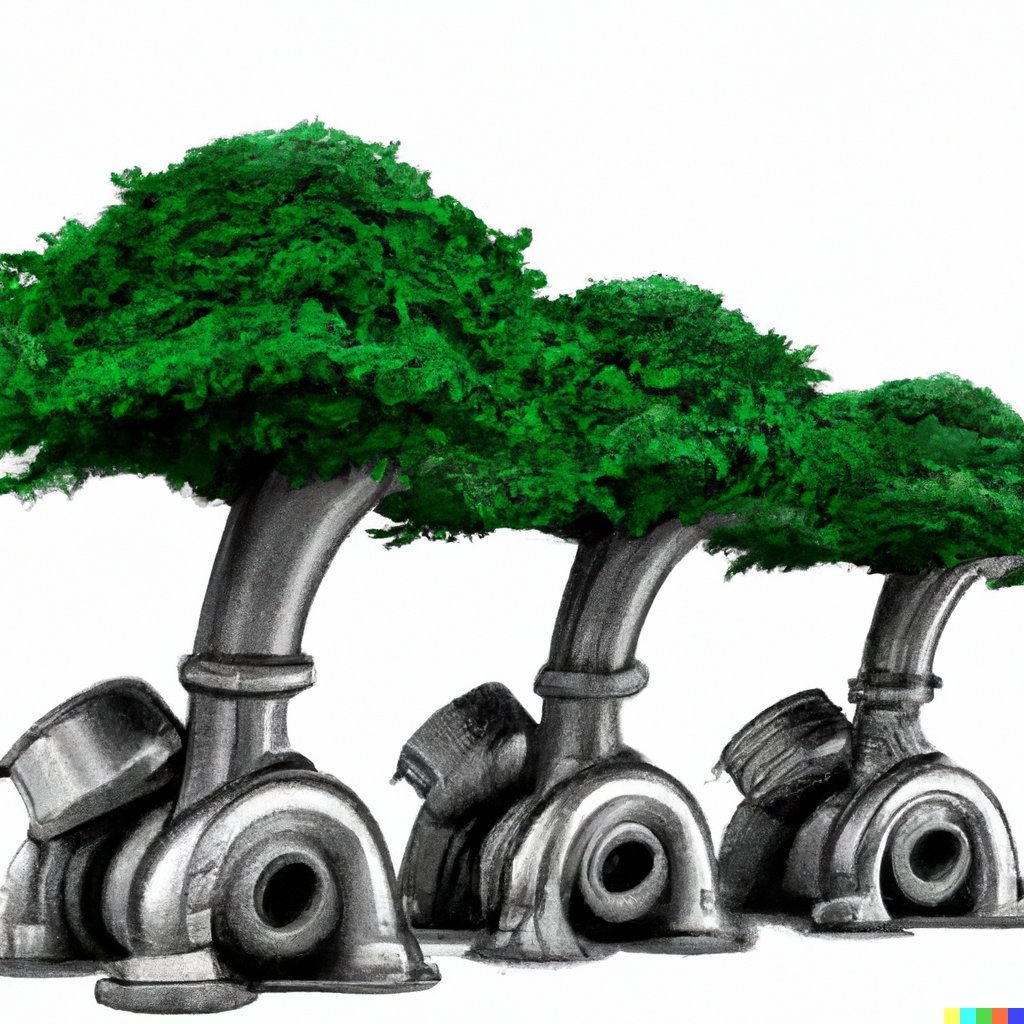
What is remanufacturing? - ARTES series 1
At its core, remanufacturing is the process of taking a component that has been in service and returning it to an as-new, or better, condition and performance. Replacing wear items such as seals and bearings can breathe new life into a component, extending its useful life and preventing the need for a full replacement. This has numerous benefits to the product lifecycle including reduction in waste, reduced reliance on raw material supply chains, and shorter lead times for remanufactured vs. new components.
Before remanufacturing, worn or damaged components must be identified and disassembled. This can be a time-consuming and costly process, often performed entirely manually by a skilled operator. As a result, remanufacturing is typically confined to high-value components with large cast alloy elements or intricate machined features. By embracing state-of-the-art processes that boost speed and efficiency of disassembly, it is possible to develop a robust business case for remanufacture of a wide spectrum of parts – turbochargers, hydraulic cylinders, landing gear, electric vehicle (EV) battery packs and more.
In the UK, the remanufacturing industry has a potential market size of £5.6 billion [2], £2.2 billion of which is attributed to passenger cars. This market is largely based on continuing to use existing remanufacturing methods that are significantly less high-tech than what is seen in new manufacturing. To eliminate scrapping of potentially useful components, the remanufacturing sector must catch up with the technological leaps that have been made in CNC machining, laser processing and additive manufacturing. Huge rewards can be found in the automotive and aerospace sectors, where nickel superalloy or aluminium components with high embedded energy are scrapped simply because the cost to disassemble and replace wear parts is too high. The fasteners (nuts, pins, rivets) holding these components together are the first barrier to remanufacturing and are the first target for Scintam in our mission to automate the remanufacturing process.
The remanufacturing market is increasingly driven by government policy across Europe, adding pressure on manufacturers to increase environmental sustainability. The established markets in the UK and Germany are expected to grow at a fast pace, with smaller remanufacturing markets in the Netherlands, France and Scandinavia also seeing a large boost. This is in part driven by the ‘Fit for 55’ EU policy which aims to reduce carbon emissions by 55% by 2030, alongside the EU End-of-Life Vehicle Directive that encourages responsible re-use and recycling of automotive components. Despite the increasing uptake of EVs, combustion engine components will remain an important part of the mix – the volume of remanufacturing of turbochargers, transmissions and engines in the automotive industry is expected to increase by 3-15% by 2025. The increasing market share of EV’s brings new technical challenges to the remanufacturing sector, requiring innovative solutions for truly sustainable component lifecycles. This is an ideal time to introduce new technologies that make the disassembly and remanufacturing of EV components faster, safer and at lower cost.
Adaptable, automated machines hold the keys to unlocking commercially viable remanufacturing on a large scale. This philosophy is at the core of Scintam’s new ARTES system. We will ensure that components can be easily disassembled, even if they were not designed with this in mind. But, to achieve our combined goal of a sustainable component lifecycle, manufacturers and solution providers like Scintam must work together to develop the technologies that really push the remanufacturing industry forwards.
[1] https://doi.org/10.1016/j.jengtecman.2013.11.002
[2] https://www.carbontrust.com/news-and-events/insights/supply-chains-are-shaping-the-business-models-of-the-future
About Scintam Engineering
Scintam develops cutting-edge repair, maintenance and remanufacturing tooling for a range of engineering sectors. Our pioneering technology provides environment and sustainability benefits to our customers by enabling repair instead of replacement - our aim is to maximise the number of components that are remanufactured, preventing the need for highly energy-intensive new manufacture. We design tools for aerospace MRO, and the energy and remanufacturing sectors.
Founded in March 2021, Scintam is supported by Innovate UK funding to advance our research and development capability, driving growth in the industry through the development of new technologies.